Soldabilidad de los aceros
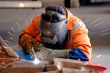
Grupo Soldadores de Mantenimiento
Soldadura de acero al carbón
1.- Aceros de medio contenido de carbón
Los aceros de medio contenido de carbón son muy fáciles de soldar. Pero deberían pre-calentarse a (175ºC - 350ºC). Deben usarse electrodos de contenido medio de carbón y bajo contenido de hidrógeno, tales como el E-6015, ó E-6016. El último numero, 5 y 6, indica que estos electrodos son de bajo contenido de hidrógeno.
2.- Aceros de alto contenido de carbón
Los aceros de alto contenido de carbono deberían ser recocidos antes de ser soldados y después de completada la suelda pueden ser tratados térmicamente a la dureza deseada. Con el fin de prevenir que el metal base se mezcle con el metal del electrodo, la penetración debe ser poco profunda. El contenido de carbón de la suelda debe ser mantenido al mínimo. Deben usarse electrodos E-6015 y E-6016. Para gran resistencia, use los electrodos E-7015 o E-7016.
Cuando suelde aceros de medio y alto contenido de carbón, la corriente debe fijarse al mínimo posible, y deposite tanto metal como sea posible en la primera pasada usando la más baja velocidad de pasada. Funda lo menos posible del metal base.
Soldadura de acero al níquel de baja aleación
El acero al níquel tiene una expansión térmica tan alta que pone al borde de causar fisuras en el cordón de soldadura mientras se enfría. Para minimizar estas fisuras, cada cordón debe ser concienzudamente golpeado con un martillo de bola.
Cuando la resistencia de la soldadura deba ser igual a la resistencia de la aleación de bajo contenido de níquel (metal base), se usa el electrodo E70-10 o E70-20. Para planchas delgadas, y poca penetración, los electrodos estándar E60-10 son los mejores. Si hay señales de fisuras, cambie por los electrodos de bajo contenido de hidrógeno, E60-15, E60-16, E70-15, E70-16.
El material grueso de acero de níquel de baja aleación debe ser precalentado a un color rojo pálido antes de soldarse
Soldadura del acero al molibdeno
El acero al molibdeno debe soldarse casi de la misma manera que el acero de medio contenido de carbón. Deben usarse electrodos para máxima resistencia. E-7010, E-7012, ó E-7020. Cuando vayan a depositarse grande áreas de soldadura, se recomiendan electrodos de bajo contenido de carbón como el E-7015 ó E-7016. Los electrodos de bajo contenido de carbón hacen innecesario el tratamiento de precalentamiento.
Cuando la resistencia no es de mucha importancia, pueden usarse electrodos de medio contenido de carbón como el E-6010. En piezas de 3/8" y mas, es necesario calentar la estructura en un horno después de la soldadura con el fin de aliviar las tensiones internas. Esto se hace calentando toda la estructura a 650 - 675ºC por el lapso de una hora por cada pulgada de espesor, seguido de un enfriamiento lento en el mismo horno a un ritmo de 90 - 120 ºC por hora.
Cuando el metal alcanza los 65ºC puede ser removido del horno y permitírsele enfriarse al ambiente con el aire en reposo.
Soldadura del acero al manganeso
El acero con bajo contenido de manganeso contiene el 2% o menos de manganeso. Al acero con alto contenido de manganeso contiene de 12% a 14 % de manganeso.
El acero de bajo contenido de manganeso puede ser soldado con electrodos que contienen un 5-10% de molibdeno como los E-7010 o E-7020. Si estos electrodos producen una penetración muy alta, el electrodo estándar E-6012 estaría bien para a menos que este produzca demasiadas crujidos al depositarse, en cuyo caso deben sustituirse con los E-6015, E-6016, E-7015, o E-7016. La penetración profunda y abundante no es conveniente porque el metal base se entremezclara con el metal de la suelda. El acero de bajo contenido de manganeso deberá ser precalentado antes de ser soldado para reducir grietas del cordón de base.
El mejor electrodo para soldar acero al manganeso es el de acero inoxidable 18-8. Use siempre la menor cantidad posible de corriente para prevenir áreas quebradizas junto a la suelda. La junta debe ser biselada y completamente limpia.
Deposite soldaduras cortas de unas 2" y permita que cada una se enfríe antes de hacer la segunda. La cantidad de calor radiado desde la soldadura debería ser lo suficientemente pequeña como para que UD pueda colocar su mano a unos 6" o 7" de la soldadura todo el tiempo. Trapos húmedos alrededor de la junta ayudarán controlar el calor.
Soldadura de aceros aleados
Las aleaciones de acero son difíciles de soldar porque las cualidades del acero aleado son fácilmente destruidas por el calor del arco y porque tienden a formarse grietas en el área de soldadura. Los electrodos usados para soldar aleaciones de acero son bajos en carbón para minimizar la formación de grietas, y los fundentes del revestimiento tienen bajo contenido de hidrógeno para reducir la posibilidad de formación de grietas bajo el cordón de soldadura.
Soldadura de acero inoxidable
El acero inoxidable es otro termino usado para los aceros al cromo y al cromo níquel. Para las planchas de acero inoxidable de calibre 20 y más gruesas, la soldadura con arco es completamente satisfactoria. Para planchas más delgadas que esta, es preferible la soldadura oxiacetilénica. En efecto, la soldadura con arco produce demasiado calor en las planchas más delgadas de acero inoxidable, y puede causar su perforación. La soldadura con gas inerte (TIG) es preferible porque elimina el peligro de destruir las propiedades de resistencia a la corrosión del acero inoxidable.
Las juntas de acero inoxidable deben espaciarse para permitir la expansión, y deben fijarse a sujetadores con planchas de enfriamiento cerca de la soldadura para disipar el calor. El acero inoxidable no conduce tan bien el calor como el acero de medio contenido de carbón, y es mas propenso a acumular calor en el área de la soldadura. Si no se tienen disponibles sujetadores, las planchas deben ser soldadas con puntos de suelda cada 1" o 2" antes de depositar el cordón principal.
Deben usarse electrodos de no más de 3/16". El contenido de aleación del electrodo debe ser siempre más alto que el del metal base con el fin de compensar la pérdida de la aleación que siempre ocurre durante la soldadura.
0 comentarios